From The Pea to The Box — Sustainable Solutions From The County of Bentheim
The Emsland Group and bekuplast have pooled their expertise and are focusing on the use of renewable raw materials in plastic products.
The sustainable use of resources and the use of environmentally friendly products has increasingly become the focus of public attention in recent years. However, this is nothing new for the two Niedergrafschaft-based companies. For them, the concept of sustainability has always been part of their corporate philosophy. This is rooted in the core business of both companies. The Emsland Group specializes in the production of native and modified starches, fibers, proteins, flakes and granulates from renewable raw materials such as potatoes and peas. The plastics processor bekuplast develops and produces sustainable reusable transport packaging. The company uses recycled raw materials to a large extent.
The two companies were already in contact through their membership of the Ems Axis. This gave both companies the idea of pooling their expertise. The common goal of both companies is to use plant fibers in the manufacture of plastic products. This project is supported by Lower Saxony’s 3N Competence Center, which promotes the use of renewable raw materials and the development of sustainable products.
For its reusable solutions, bekuplast uses various plastics made from virgin and recycled material. The proportion of recycled material has risen sharply in recent years. “Thanks to special technical processes, we can now use recycled plastics as a high-quality compound for our products. They are in no way inferior in quality to products made from virgin material,” explains Jörg Deglmann, Managing Director of bekuplast GmbH. In addition to ground used containers, plastics recovered from the Yellow Bag are also processed.
In harmony with nature, the Emsland Group creates sustainable solutions from potatoes and peas. “When developing our product portfolio, we work closely with our customers and have both the needs of the end consumer and the consistent conservation of resources in mind as well as consistent resource conservation and CO₂ avoidance,” says Dr. Julian Simke, Head of Application Technology for Technical Specialties at the Emsland Group. The delivered peas are shelled before being processed into high-quality starch and protein products. This means that the outer fibers are removed and processed separately as a valuable by-product — including for the production of plastic containers at bekuplast. In this way, the pea is used extensively so that its components can be optimally utilized and maximum added value is achieved.
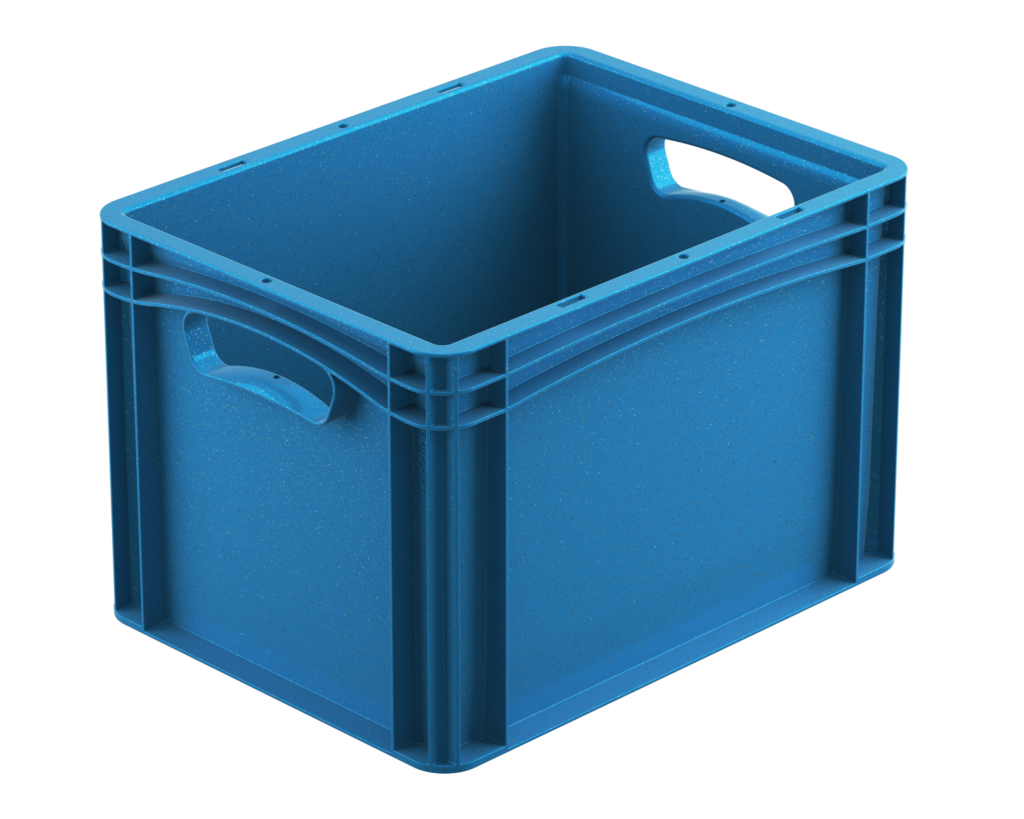
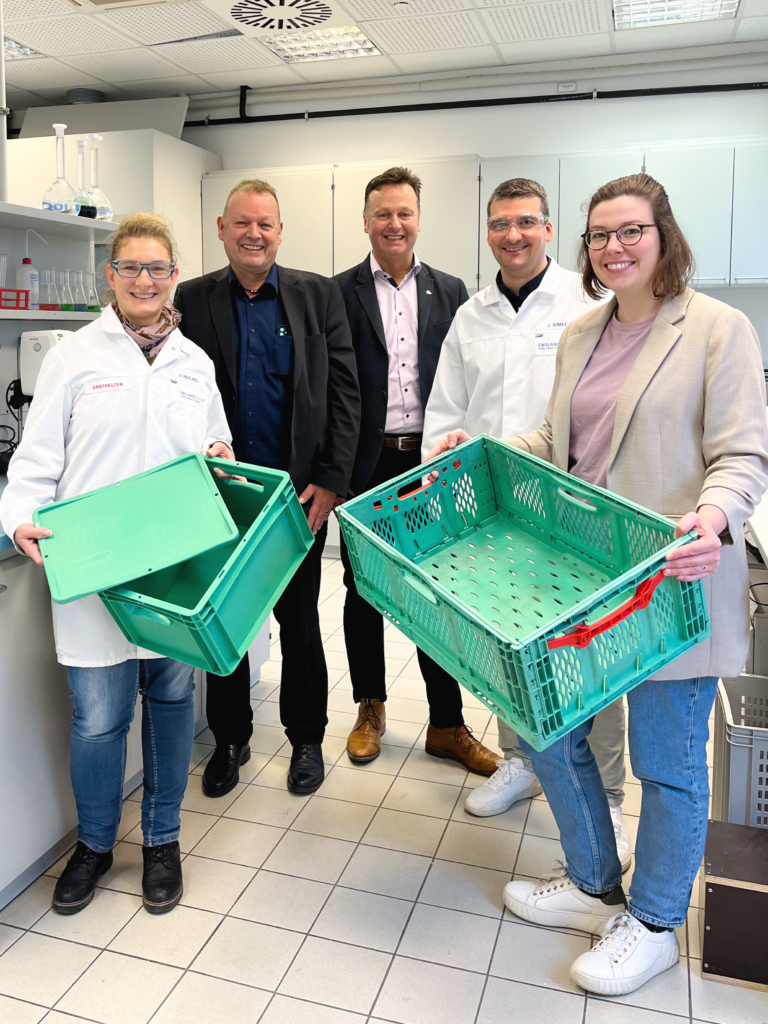
However, the use of renewable raw materials in plastic products presented the two companies with technical challenges. While plastic is usually processed at around 220 to 230 degrees Celsius, the plant-based pea fibers burn at a temperature of just 190 degrees Celsius.
In the laboratory, specially prepared fibers from the Emsland Group were tested on test machines in combination with recycled plastics. “It turned out that pea fibers are more suitable than potato fibers,” explains Maria Bollingerfähr, a member of the application technology team. In initial test productions under laboratory conditions, plastic boxes were made from pea outer shells and recycled material from the Yellow Bag, so-called post-consumer material. By using pea fiber, around 20% of the plastic material was saved and replaced by a renewable raw material. The fiber-reinforced plastic is not only sustainable, but also very stable.
After initial successful test productions on a laboratory machine, production of the first boxes was finally started at bekuplast in Ringe. “The tests with various container models were successful. We have managed to replace around 10 to 20% of the plastic in our containers with pea outer shells,” reports Jana Klein, Raw Materials Manager at bekuplast GmbH. In view of 2030, when the EU is expected to require a minimum proportion of recycled plastics in plastic products, this development is highly relevant for the future. Currently, containers made from pea fibers are still more expensive than commercially available plastic boxes, but both companies see great potential for this innovation and will continue to work on promoting sustainable solutions from the county of Bentheim.